Knittex products are made from high-density polyethylene. This is a specialised type of plastic used to produce a variety of products, including agricultural netting, making it more durable and long-lasting.
But it is still plastic, and is that not bad for the environment? Well, that is a simple question with a complex answer.
Plastic is not a bad material per se, but there are many concerns surrounding plastic. These mainly relate to the use and disposal of the materials. If plastic is used in the manufacturing process without any regard to its impact on the environment it is bad. But a company such as Knittex thinks about the responsible use and disposal of the materials they use.
This manufacturer ensures that not a single pellet of high-density polyethylene is wasted and any amount of plastic that they do not use, is disposed of responsibly.
Let us look at how Knittex ensures they reduce, reuse, and recycle their waste responsibly.
Knittex reduces plastic waste
First, this manufacturer mostly uses virgin material to manufacture a wide range of nets. This is because using unrecycled plastic makes the nets more durable. They can last much longer than any other similar product that is made from recycled materials.
Knittex exercises strict control over the batches that they produce. This allows them to recycle some of the excess material that is produced during the early manufacturing stages by melting it down and mixing it into the fresh batch without compromising the strength and durability of the product. And the proof is in the pudding so to speak. Some farmers have nets that are lasting for more than ten years! Because of this, the final product does not need to be replaced frequently, resulting in less plastic that needs to be removed from the farm and disposed of responsibly by the farmer. Nets that last longer are not only more sustainable for nature but also the farmer’s bank account!
Knittex reuses products to be more environmentally friendly
To reuse material, Knittex has devised two ways of using the textile for something other than netting. The first of these is by taking the larger sections of material that are not used and turning it into bags or covers that help protect large shipments in transit.
At the factory in Mkhuklu, factory workers sow sections of net together to form large covers for rolls of net. Due to the durability of the original product, using off-cuts in this way helps protect the customer’s order all the way from the factory to the farm. Nets that do not meet the criteria set out by the manufacturers’ strict quality control procedures fall into this category as well. Simply put, the nets aren’t just discarded, it is set aside to be used for covers, for instance, highlighting the forethought that Knittex gives to what happens to the waste the manufacturing process creates.
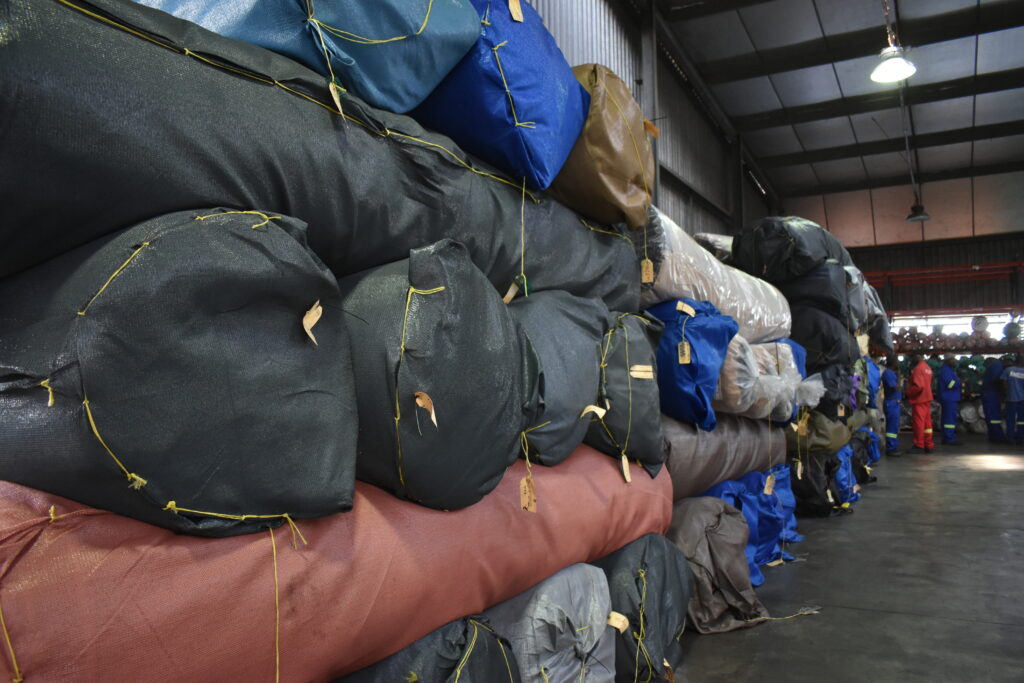
Giant rolls of net are covered in the discarded net. This protects the large rolls in the warehouse before they are shipped to other parts of the country.
In Roodepoort Knittex’s international warehouse donates small off-cuts to a lady who manufactures products from the nets.
She carefully creates patterns for a variety of products such as bags and cushion covers. This small business creates employment and reduces the waste of the nets.
Knittex recycles waste in a smart way
There are two ways in which Knittex recycles the material they use.
First, the bulk of the discarded material is sold to a South African company that specialises in making manhole covers. They melt the discarded plastic nets and add it into their mixture that forms the basis for the plastic products.
Secondly, Knittex has a recycling plant where they chop discarded pieces of net. The pieces are placed into a pelletiser that reforms pellets of polyethylene. Since the pellets are low-grade, they cannot be placed back into the factory to be made into durable netting products. Instead, these recycled pellets are added to a machine that melts it down. The melted plastic is mixed with a colouring agent (black) and sent through an extruder. In the extruder, PVC pipes are formed. The pipe is cooled down in a water tank and then cut into a set size.
The PVC pipe is used as the base that the nets are rolled onto.
It was an important investment for the manufacturer to set up the recycling plant. Acquiring the necessary equipment and skills to first process the discarded textiles into smaller chunks and then pellets, and then forming them into pipes has been a crucial step in reaching their sustainability goals.
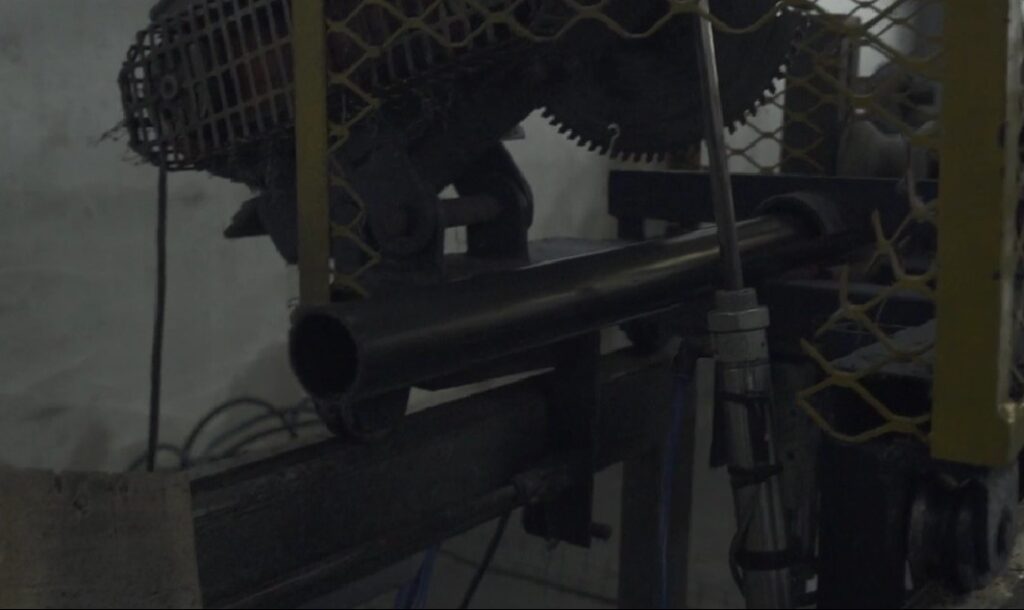
PVC pipe is manufactured from the recycled net to roll the net onto.
Now that you know how much care goes into developing products at Knittex, why not speak to the area agent near you? Reach out to them by visiting their contact page at https://www.multiknit.co.za/multiknit-contacts.html.